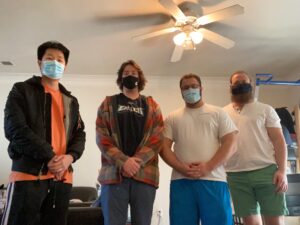
The Pennsylvania Horse Racing Association debuted its Virtual Reality Simulators to kick off 2020 at the Pennsylvania Farm Show, Horse World Expo, and at a Pittsburgh Penguins Game. After Covid-19 hit, the work did not stop on improving the VR simulators.
One thing that was missing from the harness racing simulator was the movement of the race bike. Being that nothing like this had ever been done before, there wasn’t really much of a blueprint to follow.
After some research, the PHRA reached out to the Penn State University Learning Factory for help.
The Penn State Learning Factory is a hands-on facility for engineering students to use in conjunction with capstone design and other courses, as well as research projects and student organizations. The Learning Factory provides modern design, prototyping, and manufacturing facilities, including machining (CNC and manual), 3D printing, welding, metrology, and CAD/CAM.
Through University-Industry partnerships, students design projects for clients and industry sponsors interact with students and faculty.
Working with Gary Neal, a member of the PSU Department of Mechanical Engineering and Director of Mechanical Engineering Design Projects, four students were assigned as a team to the PHRA’s project. They were Nick Patrella, a Mechanical Engineering student from Garnet Valley, PA, Billy Mellinger, a Mechanical Engineering student from White Oak, PA, Christian Cooke, an Energy Engineering major for Sea Cliff, NY, and Yuhan Dong, a Mechanical Engineering student originally from Shanghai, China who now resides in Philadelphia, PA.
Each student had the opportunity to decide which Learning Factory project they would like to be a part of. They all had their own reasons for choosing to work on the VR simulator.
Nick chose the project because he is interested in cars and racing. He has a 1991 Mustang as a project car and knowledge in vehicles, so the sulky sparked his interest.
Billy and Christian both thought compared to the other options to pick from it was a very “outside of the box” project and seemed like it would be fun.
Yuhan said he chose the project because he is a sim-racing driver. He said that while a motion simulator for sim-racing is expensive, this project helped him to gain more knowledge on motion simulators so that he could maybe build his own sim-racing simulator in the future.
Each student was assigned a role within the team. Nick acted as Project Manager, Christian Cooke was Journal Keeper, Billy Mellinger as Note Taker, and Yuhan as the Scheduler/Budget Keeper.
The team had a weekly call with the PHRA to discuss progress and anything else that may have come up in the week prior. They also sent detailed progress reports each week so that the PHRA could see the progress they were making.
Of the four team members, none of them had any experience in harness racing prior to this project. The PHRA wanted to give them the experience of driving a jog cart at one of PA’s local training farms. This helped the team get a feel for what they needed to simulate. Each student went for a jog cart ride to feel the movement for themselves.
After the jog cart rides, the race bike used for the simulator was moved to Penn State so that the team could begin working on it. It was quickly decided that an electric motor would be the best way to go. The main issues would be creating a design that allows the bike to move side to side and up and down but at the same time not allow it to move across the floor and making a design that would be able to support an adult sitting on the bike.
Working with a tight time constraint, Covid restrictions, and a budget that left little room for error the team quickly worked to overcome any obstacles that came up.
All of them said that the biggest challenges were being able to complete the project with access to the PSU facilities limited due to Covid-19, along with staying on budget and machining the steel.
The final design ended up being a wooden platform with the motor and axles attached to the platform. The tires of the race bike sit on the cylinders at the end of each axle.
With this design, the old wheel chocks which held the race bike in place could no longer be used as they too sat under the wheels. Flint Road Welding of Mifflintown was able to design new chocks that sit in front and behind the wheels. These chocks have conveyor belt-like rollers that allow the wheel to turn but for the race bike to remain stationary.
Nick said that this project helped him learn various skills, such as how to be a leader, working with a budget and schedule, and working with the materials are given to you.
“For example, due to the circumstances of COVID-19, the team was limited in tools and time allowed in the machine shop. As stated previously, my mechanical background and having older vehicles, I carried an assortment of common hand tools in the trunk of my car. Using these common hand tools, the entire project was assembled. The components were machined to specific tolerances in the machine shop, but looser tolerance holes were drilled on a drill press in my apartment. The platform was cut with a handsaw and screwed in by hand. Shaft alignment was accomplished by using an inclinometer and a dial indicator. Due to time constraints, limited machine shop accessibility, and other various circumstances, critical decisions had to be made and acted upon, such as partially manufacturing and completely assembling the project outside of the Learning Factory. It opened my eyes to what can really be accomplished by individuals and a team.” he said.
Billy and Christian both said that this project taught him that machining can take a very long time, often longer than one would think.
Yuhan said that one of the biggest things he learned is that it is always good to thoroughly research and do your calculations before purchasing any parts.
Looking back, Nick said that this was the kind of project that he had been looking forward to since his freshman year. He couldn’t wait for a hands-on assignment and enjoyed seeing this entire process unfold from the early stages to the assembly and to the testing of the simulator. He also appreciated that the PHRA gave the team their full trust in coming up with the design.
The finished simulator is not what anyone envisioned when they started. Christian said that the final project is much more simple than he had pictured, but that’s a good thing in this case considering that the realism is still there. Billy said he also had been envisioning something more complex.
Yuhan said that the finished project is what he foresaw when the process started and it is one that he is very proud of.
Nick went on to say that it was not at all what he pictured. He said after doing an immense amount of research on simulators that he was thinking of many different concepts. “As a team, the final concept, which became the prototype, was based on a custom design of a cam system to create a cyclic lifting action for each wheel of the sulky.” he said.
While none of the team members really had an interest in horse racing, all of them said they are interested in going to the track now.
Nick has always been interested in the general concept of racing. “The adrenaline is unlike anything else. From a basic foot race to racing cars, it has always been interesting” he said.
While he was never involved with horse racing, he said researching this project sparked his interest and he is definitely interested in going to nearby Harrah’s Philadelphia.
Billy never really had an interest in attending the races prior to this project, but after researching it he said he definitely is now, as it can be very exciting.
Christian said that he never realized how amazing horses are. He and Yuhan both also said they also would now be interested in going to the track.
Nick went on to say that he thoroughly enjoyed working alongside the PHRA and that this was a great experience. He is excited to see the project in use after Covid-19 and to stay in touch with the PHRA.
He also wanted to thank the professionals at the Learning Factory and their professor, Gary Neal.
After graduation, he plans to enter the workforce in Mechanical Engineering. Ideally, he is interested in a job at a small firm where he could work on one project from start to finish and learn throughout the process. He likes being hands-on and enjoys both designing and creating projects.
Yuhan said that after he graduates from PSU, he plans on continuing his education by pursuing his master’s degree in robotics.
Christian plans to take next year off and then reviewing the energy markets to see where they are at.
Billy plans to find a job in something related to manufacturing upon graduation.
Gary Neal felt this was a great project for the Learning Factory and the students. “PHRA’s original objective and scope for the project were perfect! The sponsor, Mr. Seth Dowling, was enthusiastic, responsive, and went out of his way to help the team be successful. This student team combined knowledge and skills from multiple disciplines including mechanical engineering, electrical engineering, manufacturing engineering, and energy engineering, and the student team did a fantastic job! They went through the standard design process but customized that process to this specific project. They overcame initial challenges, and through the team’s use of iterative prototypes, really refined their ideas, and in the end, created a functional final product. Their ability to create these hands on prototypes and final product, given the COVID challenges, shows the dedication and perseverance of the sponsor and Penn State engineers.”
Pete Peterson, President of the PHRA, said “It is always nice when the industry can team up with educational institutions across Pennsylvania. This was a true win-win through my eyes. The students were able to get experience with a hands-on project and in return the PHRA got harness racing’s first motion Virtual Reality Simulator.”
The Learning Factory looks for projects each semester. With junior engineers from every discipline available, they are able to staff projects for any type of engineering project that contains design content. In particular, they look for projects that cross typical engineering bounds. According to Gary “This opportunity to work on multidisciplinary projects gives students a skill and experience that is valuable when they graduate and move into the workforce.”
For more information about the Learning Factor and for information on sponsoring a project, visit the PSU Learning Factory website here.